Footnotes to Fashion: How Innovation in Antique Sewing Machine Feet Shaped Garment Construction Techniques
The hum of a vintage sewing machine – a comforting, rhythmic pulse echoing from a bygone era. It’s a sound often associated with quiet industry, with the creation of something beautiful and lasting. But what many overlook is the quiet revolution happening *under* the needle: the evolution of the sewing machine foot. More than just a small piece of metal, these feet represent ingenious solutions to complex challenges in garment construction, acting as footnotes to the story of fashion itself. They’re tangible links to a time when ingenuity and craftsmanship were paramount, and each curve and angle whispers tales of innovation.
My own fascination with antique sewing machine feet began with a dusty box inherited from my grandmother. It wasn't filled with jewels or treasures, but with a collection of these small, often overlooked tools. There was a plain, universal foot, a zig-zag foot encrusted with years of accumulated thread, a buttonhole foot that felt heavy and significant in my hand. Examining them, I began to understand that each one wasn't just for sewing; they were emblems of a changing landscape in garment making. They represent a period of remarkable advancement, fuelled by the desire to make clothes more efficiently, more precisely, and more beautifully.
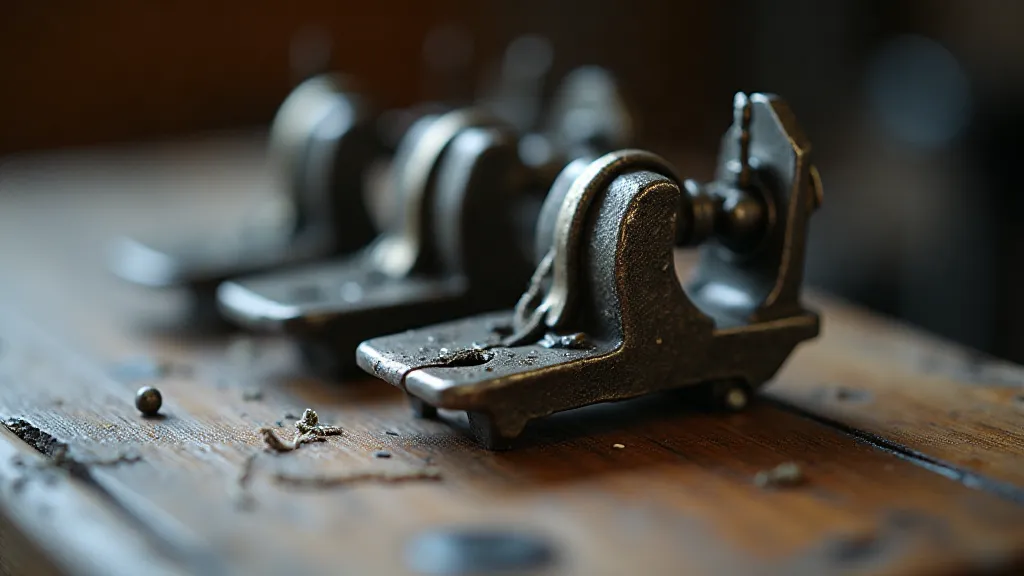
The Early Days: The Universal Foot & Basic Needs
Early sewing machines, dating back to the mid-19th century, were often equipped with a simple, universal foot. These feet were essentially a flat plate, designed to guide the fabric under the needle. While functional, they were limited in their capabilities. They worked best with medium-weight fabrics and straight stitching, leaving intricate details and specialized tasks to painstaking handwork. Think of the elaborate Victorian gowns - the complex ruffles, the precisely gathered sleeves, the tiny pleats; much of this was achieved *before* the garment even reached the sewing machine.
The advent of the Singer sewing machine in the 1850s marked a significant moment, but even with its advancements, the need for specialized feet soon became apparent. Garment patterns were becoming more complex, and the demand for faster, more efficient production grew. The desire to move beyond the limitations of the universal foot spurred innovation – a period of remarkable creativity within the seemingly small domain of sewing machine attachments.
The Rise of Specialized Feet: Meeting the Demands of Emerging Styles
The late 19th and early 20th centuries witnessed an explosion of sewing machine foot designs. As fashion trends shifted – think of the streamlined elegance of the Edwardian era, followed by the bold, geometric styles of the 1920s – so too did the need for specialized feet. The buttonhole foot, for instance, initially a cumbersome attachment requiring significant skill, evolved into more refined versions that could produce neat, consistent buttonholes. This was transformative, freeing up valuable time and reducing the reliance on hand-sewing for a tedious, repetitive task.
The gathering foot, designed to ease the process of creating ruffles and gathers, was another crucial innovation. Think of the layers of fabric defining the Gibson Girl silhouette; a gathering foot made recreating that volume significantly easier. Darning feet, originally intended to repair damaged fabric, also found a place in creating intricate decorative stitching. And the zipper foot, a relatively later invention, revolutionized the construction of garments with closures, a style becoming increasingly popular in the early to mid-20th century.
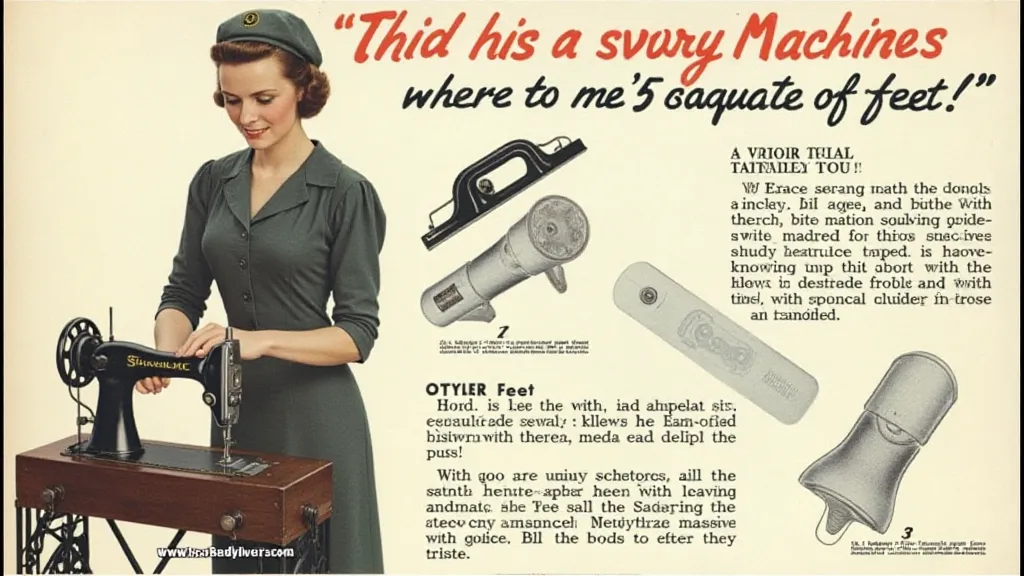
The Craftsmanship Within: More Than Just Metal
Examining antique sewing machine feet, one can appreciate the level of craftsmanship involved. These weren't mass-produced objects churned out by machines. They were often hand-filed, carefully shaped, and meticulously finished. The edges are often subtly rounded, a testament to the attention paid to detail. You can almost *feel* the touch of the artisan who shaped them. They're solid, weighty objects – built to last, a stark contrast to many of today’s disposable tools.
The materials used also tell a story. While most are made of steel, some rare feet are made from bronze or even silver. These were often reserved for high-end sewing machines, reflecting the owner's commitment to quality and precision. Even the smallest scratches and imperfections on these feet are reminders of the countless garments they helped create – silent witnesses to the ebb and flow of fashion history.
Collecting & Restoration: Preserving a Legacy
Today, antique sewing machine feet are becoming increasingly sought after by collectors and restoration enthusiasts. They represent a tangible link to a bygone era – a time when craftsmanship and ingenuity were paramount. A collection of these small tools can tell a fascinating story about the evolution of garment construction and the relentless pursuit of innovation.
Restoring these feet can be a rewarding experience. Often, a simple cleaning with a specialized lubricant can remove decades of accumulated grime and bring out their original luster. More complex restorations might involve re-filing worn edges or replacing broken components – a labor of love for those who appreciate the history and artistry of these small tools.
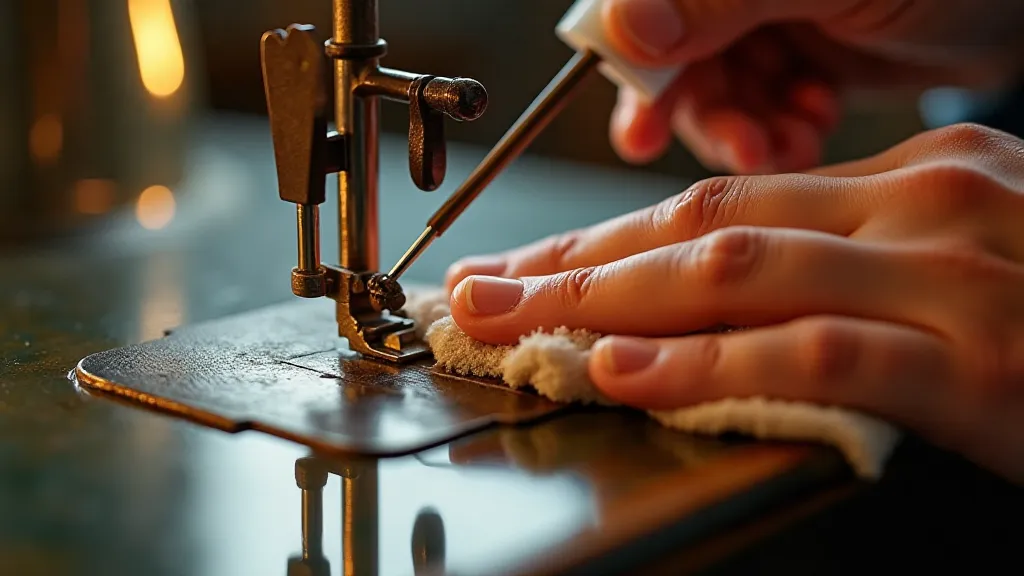
The Enduring Relevance
While the world of garment construction has evolved dramatically, the basic principles remain the same. The ingenuity of the antique sewing machine foot designers resonates even today. They remind us that even seemingly small innovations can have a profound impact on a craft. They offer a glimpse into a past where function and artistry were intertwined – a legacy that continues to inspire and inform contemporary sewing practices. And, perhaps most importantly, they offer a tangible connection to the dedicated individuals who shaped the world of fashion, one stitch at a time.