Glimpses of a Loom's Soul: Mapping the Geographic Spread of Sewing Feet
There's a quiet beauty in holding a vintage sewing machine foot. More than just a small piece of metal, it’s a tangible echo of ingenuity, a tiny testament to the ceaseless human drive to simplify and enhance a craft. I remember the first time I truly *looked* at one – a delicate, slightly worn satin stitch foot for a Singer 201. It wasn't about the sewing itself, but the feeling of holding something that had lived a life, participated in countless creations, and quietly endured the passage of decades. Now, imagine expanding that feeling to encompass the landscape of these miniature marvels – scattered across continents, subtly different, each revealing a glimpse into a specific moment in time and place.
We tend to think of sewing machine feet as standardized, universal accessories. And in a modern context, they are. But step back into the late 19th and early 20th centuries, and you discover a fascinating patchwork of regional designs, manufacturing quirks, and even localized needs that shaped their evolution. This isn't just about identifying a foot; it's about using it as a cartographic key to unlock stories of industrial adaptation, craft traditions, and the global flow of technology.
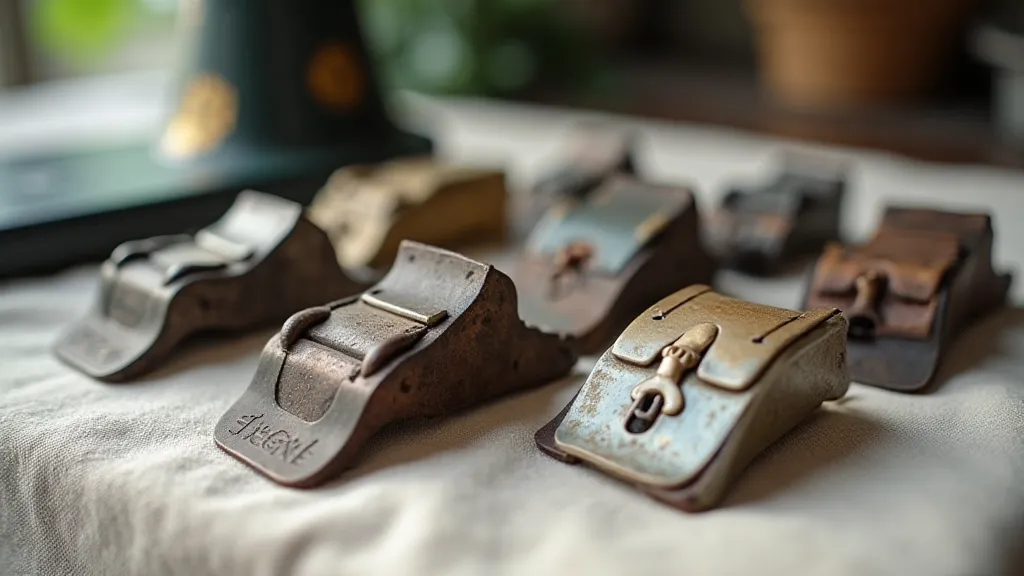
The Seeds of Innovation: Europe and the Dawn of Mass Production
The origins of mass-produced sewing machines, and consequently their accessories, are deeply rooted in Europe. Figures like Barthelemy Thimonnier in France and Isaac Singer in America (who built upon existing European patents) revolutionized textile production. Early European manufacturers, particularly in Germany, England, and Switzerland, focused on precision engineering and high-quality materials. Their feet, often crafted from solid brass or steel, were robust and reflect a practicality born from the demands of burgeoning factories. You're likely to find more intricate detailing, hand-finished edges, and a certain elegance in these early European feet – a subtle nod to the prevailing design aesthetic of the time.
German manufacturers, known for their meticulous approach, frequently produced specialized feet catering to the region’s strong tradition of tailoring and embroidery. Consider the “buttonhole foot” – a relatively simple device, yet variations abound in the early German examples. Some feature intricate, almost ornamental embossing along the edge, showcasing a level of detail rarely seen in American counterparts. This reflects not only a manufacturing specialty but also the cultural value placed on craftsmanship and aesthetics within the German textile industry.
England, at the heart of the Industrial Revolution, saw a rapid proliferation of sewing machine manufacturers. Here, practicality reigned supreme. Feet tended to be more utilitarian, designed for efficiency and mass production. The focus was on getting the job done, and any decorative flourishes were often secondary. However, the sheer number of manufacturers meant a wider variety of designs emerged, reflecting the diverse needs of the British textile market – from high-end tailoring in London to the production of sturdy workwear in the industrial north.
Across the Atlantic: American Ingenuity and the Rise of Standardization
The arrival of sewing machines in America spurred a new wave of innovation. While initially reliant on European designs, American manufacturers quickly began adapting and refining them, often driven by the needs of a rapidly expanding consumer market. The focus shifted towards affordability and standardization. This led to a simplification of designs and a greater reliance on cast metal parts, which, while less aesthetically pleasing to some, significantly reduced production costs.
The dominance of the Singer Sewing Machine Company had a profound influence on the standardization of sewing feet in America. Singer’s widespread distribution network meant that their designs became, in essence, a de facto industry standard. While other manufacturers continued to produce feet, many followed Singer’s lead, resulting in a more homogenous appearance compared to the earlier European models. This isn't to say American feet lacked ingenuity. Quite the opposite. American manufacturers were remarkably adept at developing specialized feet that catered to the unique demands of the American textile market – from quilting to leatherworking.
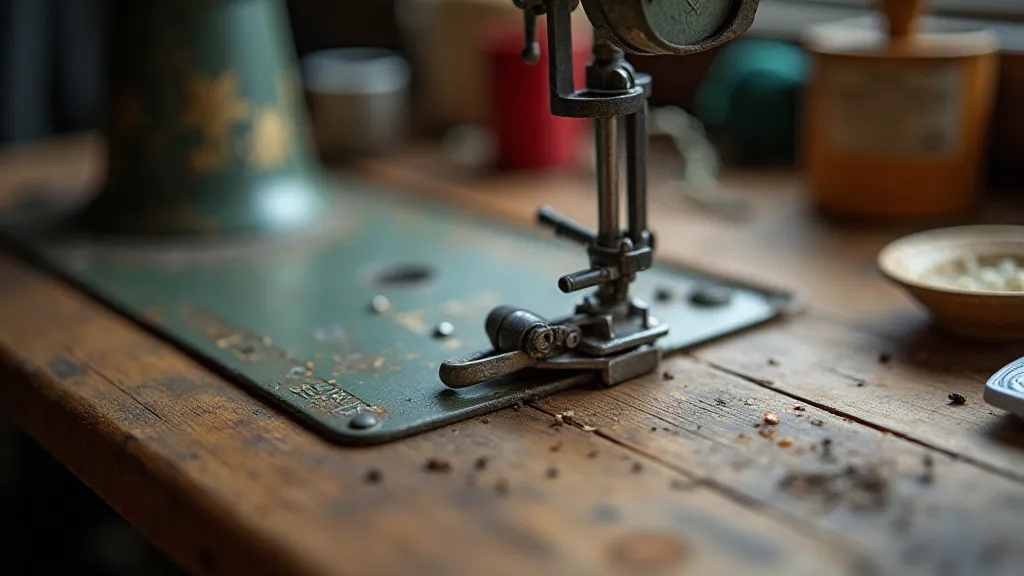
Regional Quirks and the Story They Tell
Delving into the regional variations is where the true cartographic narrative begins to emerge. For example, in areas with a strong quilting tradition, like the American Midwest, you’re more likely to encounter specialized quilting feet – often simpler in design but exceptionally durable – reflecting the demands of producing large, complex quilts. Similarly, regions with a thriving leatherworking industry, such as certain areas of Pennsylvania, often saw the development of specialized leather feet, designed to handle the thicker, more demanding materials.
Consider the "zigzag foot" – a seemingly simple invention. While the underlying principle was patented in Europe, the specific designs found in North America often incorporated subtle variations in the angle and shape of the guide, reflecting the different sewing techniques and garment styles prevalent in the region. Even the materials used could vary. While brass was common across the board, some manufacturers in regions with limited access to brass substituted iron, resulting in feet that are heavier and more prone to rust, but nonetheless a fascinating piece of local industrial history.
Rarity and the Collector’s Perspective
The rarity of a particular sewing machine foot isn’s just a matter of how few exist. It’s inextricably linked to its geographic origin and the historical context in which it was produced. A foot manufactured by a small, regional company in Germany in the 1880s is likely to be far rarer than a mass-produced Singer foot, even if the Singer foot is in better condition. The wear and tear a foot has experienced also tells a story – a chipped guide might indicate it was used extensively for a challenging project, a rusted shank might suggest it was stored improperly, but each mark contributes to the foot’s unique history.
The collecting of antique sewing machine feet isn't just about acquiring objects; it’s about uncovering fragments of a larger narrative – a narrative of industrial ingenuity, regional adaptation, and the enduring human drive to improve the craft of sewing. Each foot is a tiny window into the past, offering a glimpse into the lives of the people who made them, used them, and passed them down through generations.
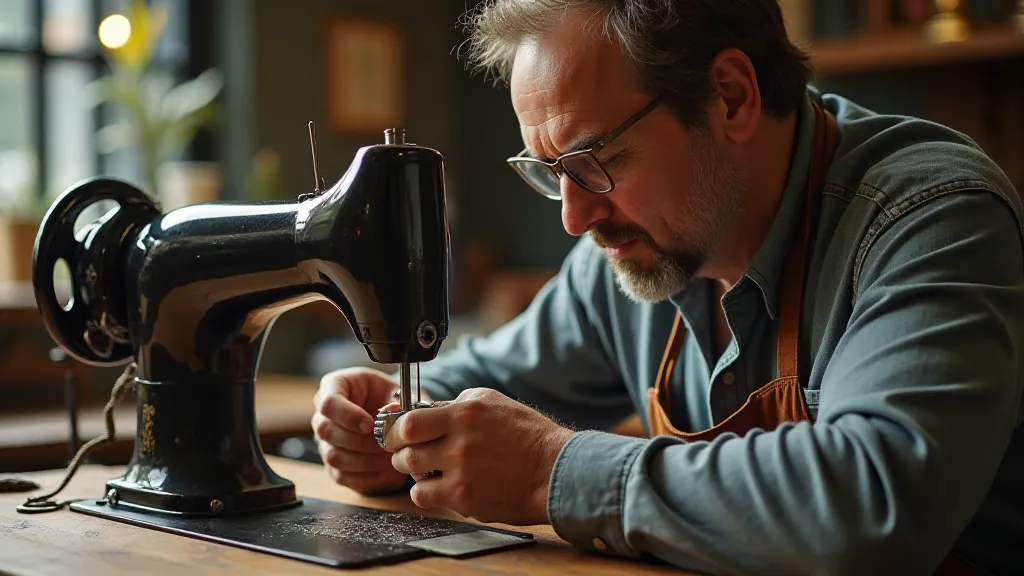
By studying the distribution and characteristics of these humble accessories, we can gain a deeper appreciation for the complexity and richness of the sewing machine’s history – a history far more nuanced and fascinating than often perceived. It’s a cartography of creativity, etched in metal, waiting to be deciphered.