A Metallic Requiem: Assessing the Repairability of Antique Sewing Machine Feet
There’s a peculiar melancholy that settles over a collection of antique sewing machine feet. Each tiny, intricately shaped piece whispers stories of hands long gone, of garments meticulously crafted, of lives lived and families clothed. They are miniature testaments to an era when durability meant something, and craftsmanship wasn’t a buzzword, but a tangible reality. To hold one, to examine its wear, its imperfections, is to connect with a lineage of artistry that feels increasingly distant in our age of mass production.
My own fascination began with a basket overflowing from my grandmother’s attic. Amongst yellowed linens and chipped porcelain, I found them: a jumble of metal appendages, dull with age but possessing an undeniable charm. I knew, instinctively, that these weren’s just “sewing machine feet.” They were fragments of history, silent witnesses to decades of domestic life.
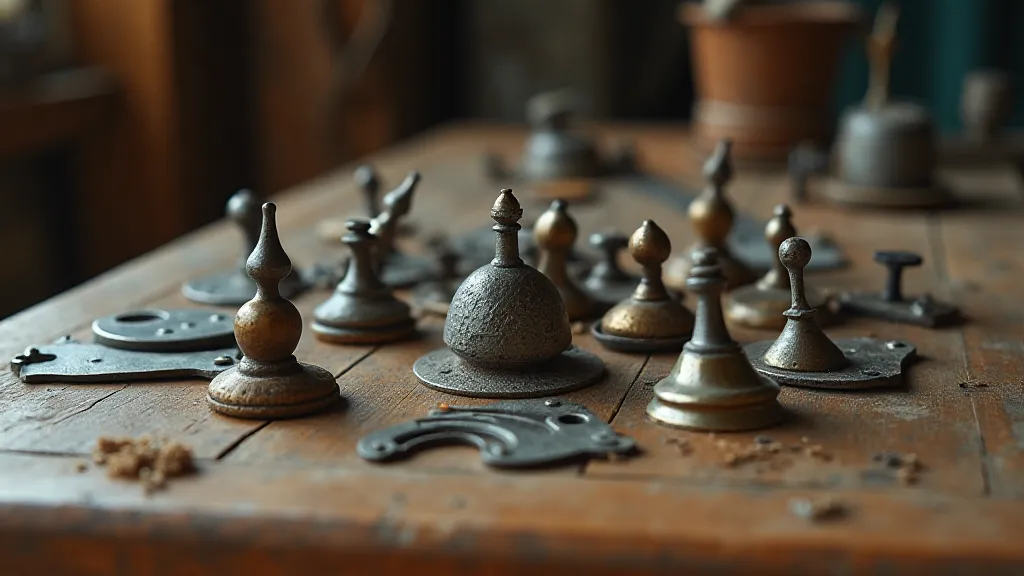
The Anatomy of a Vintage Foot: More Than Just Metal
Before we delve into repairability, understanding the construction is crucial. Early sewing machine feet weren't the interchangeable, mass-produced items we know today. They were often integral parts of the sewing machine head, sometimes riveted or permanently affixed. Even the later, more ‘modular’ feet, were built with a level of precision that demands respect. You're not dealing with stamped-out blobs of metal; you're often looking at hand-filed, precisely shaped components.
The materials themselves tell a story. Early feet were primarily made of brass or steel. Brass is softer and more prone to wear, resulting in a distinctive patina – a surface discoloration that’s often the mark of a long and useful life. Steel was (and is) harder, capable of withstanding more abuse, but also susceptible to rust and corrosion. Iron was sometimes used, particularly in the very earliest machines, but it’s notoriously susceptible to rust and requires careful handling.
Assessing the Damage: A Gentle Examination
The first step in assessing repairability is a thorough visual examination. Don't rush. Use good lighting and, if possible, a magnifying glass. Look for cracks, breaks, significant bends, or signs of excessive corrosion. A small amount of wear is perfectly normal and even desirable – it adds character and tells a story. However, structural damage necessitates a more careful approach.
It’s surprising how many “broken” feet can be salvaged. Often, what appears to be a catastrophic break is merely a fatigue crack, a result of repeated stress over decades of use. These cracks can sometimes be carefully repaired (more on techniques later), though a perfect restoration isn’t always possible – nor is it always necessary. A visible repair can be a beautiful testament to the piece's history and its resilience.
Repair Techniques: A Craftsman’s Touch
Repairing antique sewing machine feet isn't a process for the faint of heart. It requires patience, skill, and a willingness to experiment. There's no one-size-fits-all solution; each case demands a bespoke approach.
Welding: For clean breaks, TIG welding can be remarkably effective. The heat needs to be carefully controlled to avoid damaging the surrounding metal and altering its temper. It’s a technique best left to experienced welders who understand the nuances of working with thin metals.
Brazing: Brazing offers a slightly lower temperature option compared to welding, making it suitable for feet made from softer metals like brass. The bond is strong, but the brazed area will be clearly visible, which some collectors might find undesirable. It’s an excellent option when a truly invisible repair isn’t the primary goal.
Epoxy Bonding: For smaller cracks and hairline fractures, a high-strength epoxy can be surprisingly effective. Surface preparation is *critical*; the surfaces must be impeccably clean and roughened to ensure a strong bond. It's not as structurally robust as welding or brazing, but it can prevent further deterioration and stabilize a weakened foot.
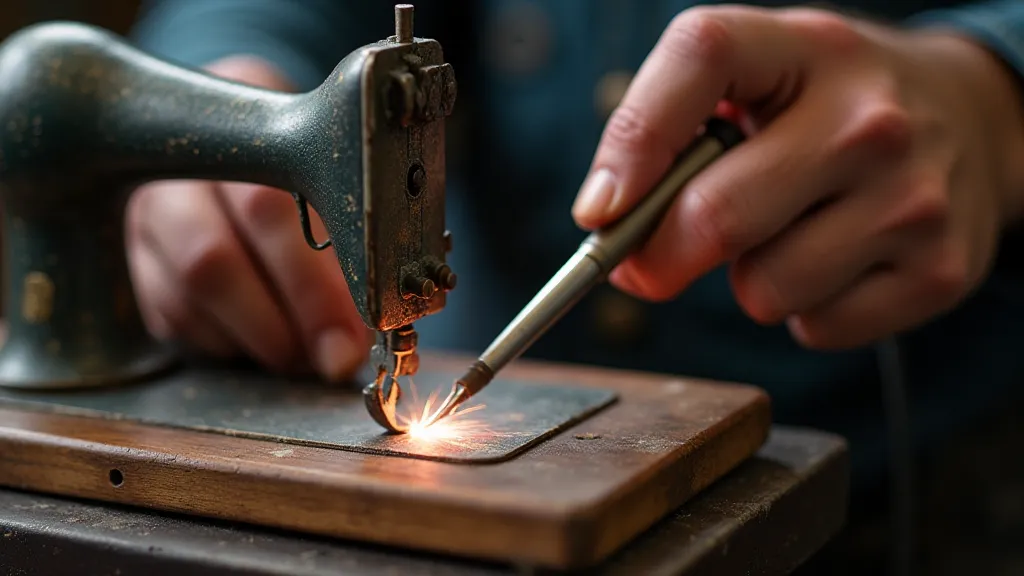
The Ethical Considerations: Preservation vs. Perfection
This is perhaps the most important aspect of repairing antique sewing machine feet. There’s a debate to be had about the ethics of restoration. Some collectors prefer "as-found" condition, believing that any alteration diminishes the historical integrity of the piece. Others believe that stabilizing and preserving a fragile artifact is a worthwhile endeavor, even if it means a visible repair.
My personal philosophy leans towards preservation. I believe these objects were meant to be used, not simply admired from afar. A visible repair, done with skill and respect, is a reminder of the foot's past life and its ongoing story. It’s a mark of resilience, a testament to the enduring power of craftsmanship.
Beyond Repair: Celebrating the Imperfect
Sometimes, a foot is simply too damaged to be repaired. The metal may be too brittle, the break too complex. In these cases, rather than discarding the piece, consider alternative uses. A collection of damaged feet can be repurposed into unique jewelry, miniature sculptures, or even incorporated into mixed-media artwork. The possibilities are limited only by your imagination.
There’s a profound beauty in the imperfect. These tiny, metallic fragments are more than just sewing machine accessories. They are echoes of the past, whispers of lives lived, and enduring symbols of human ingenuity. Even in their brokenness, they hold a unique and compelling charm. And the understanding of that charm is a form of appreciation, a form of keeping history alive.
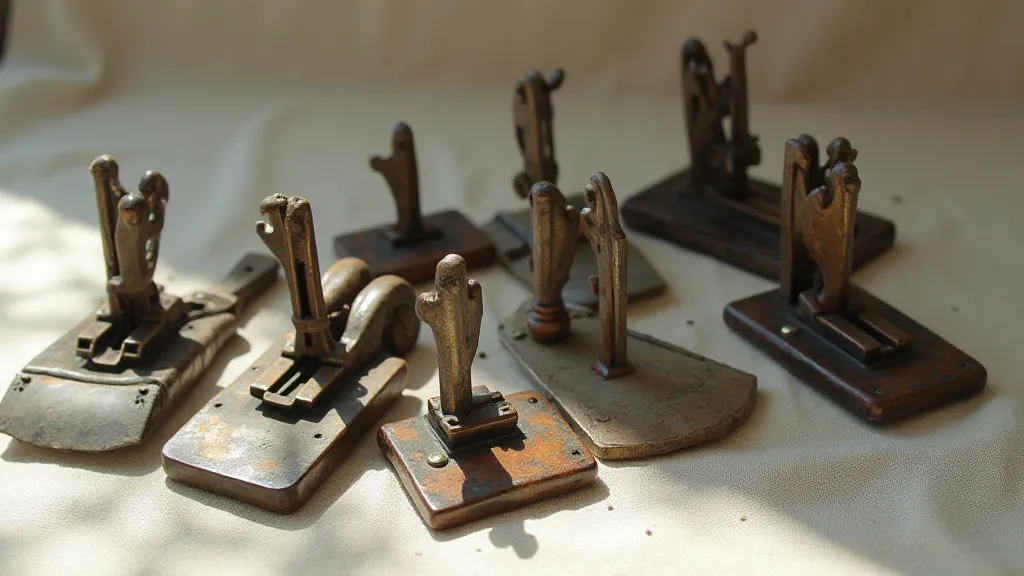