Chromatic Reflections: The Evolution of Color & Finish on Vintage Sewing Feet
There's a quiet poetry in holding a vintage sewing machine foot. It’s more than just a piece of metal; it's a tiny artifact, a witness to generations of creativity and ingenuity. Each mark, each subtle variation in finish, whispers a story of the maker, the machine it served, and the hands that guided it. My own fascination with these diminutive tools began years ago, not with a grand ambition of collecting, but with a simple appreciation for the small, often-overlooked details that reveal so much about a bygone era.
Imagine a world before mass-produced everything. When quality wasn't just a marketing buzzword, but a fundamental expectation woven into the very fabric of creation. The sewing machine feet of the late 1800s and early 1900s were tangible representations of this ethos. They weren’t stamped out by the hundreds; they were painstakingly crafted, often by hand, reflecting a commitment to both functionality and aesthetic appeal. And much of that appeal was inextricably linked to the colors and finishes applied.
The Early Days: Brass and the Promise of Polished Beauty
Initially, the vast majority of sewing machine feet were made from brass. Brass was readily available, easily worked, and possessed a warm, inviting tone. The early manufacturing processes involved substantial polishing, resulting in feet that shone with a lustrous glow. This wasn't just about aesthetics; the polished surface also served a practical purpose. It reduced friction against the fabric, contributing to the machine’s efficiency. Looking at these feet today, even those showing signs of age, evokes a sense of warmth and elegance. The patina, that subtle darkening that time imparts, only adds to their character, revealing the years of faithful service.
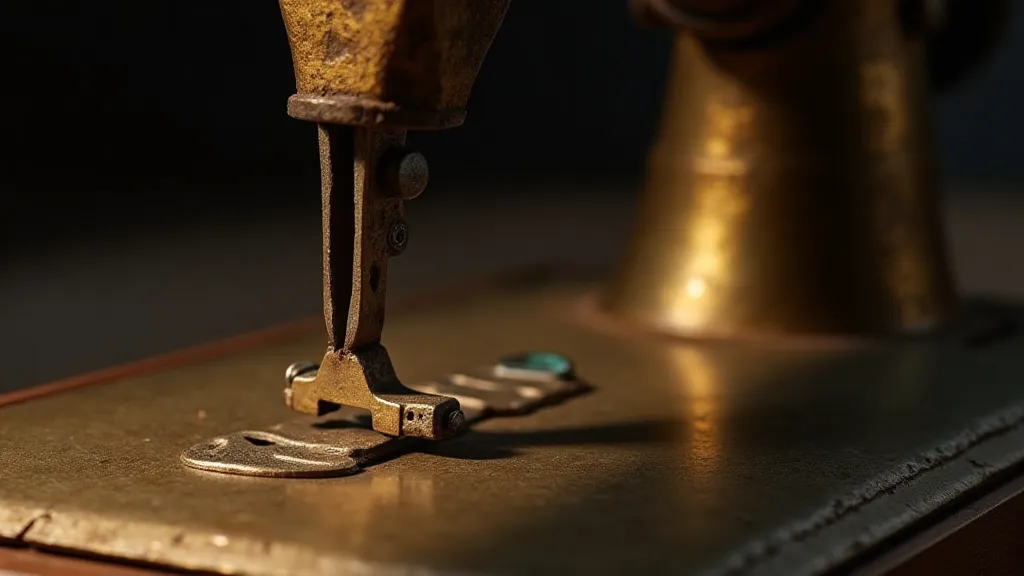
The Rise of Steel and the Introduction of Bluing
As manufacturing techniques evolved, steel became increasingly common. Steel offered greater strength and durability, essential for the heavier, more complex sewing machines being developed. However, raw steel is prone to rust, a significant drawback. The solution? Bluing. This process involved immersing the steel in a hot, alkaline solution that created a thin layer of black iron oxide on the surface. The resulting finish wasn’t just protective; it possessed a distinctive, almost regal appearance. Blued steel feet became synonymous with a certain level of quality and refinement.
I remember finding a box of these blued feet at an estate sale years ago. The way they gleamed in the dim light, a silent testament to a time when things were built to last, was truly captivating. Each foot was different, subtle variations in the bluing indicating the hand of the person who applied it. It’s these small imperfections, these unique signatures, that make collecting – or even simply appreciating – vintage sewing feet so rewarding.
Nickel Silver: A Glimmer of Modernity
Around the turn of the century, nickel silver (an alloy of copper, nickel, and zinc) began to appear. Nickel silver offers a bright, silvery-white finish that was considered quite modern and fashionable. It’s remarkably resistant to tarnishing compared to both brass and steel, making it a popular choice for feet intended for heavy use or for machines targeted at a more discerning customer. Nickel silver feet often have a more machined look, reflecting the increasing reliance on automated processes in manufacturing. However, even within this seemingly uniform material, subtle differences in finish can be observed, from highly polished surfaces to slightly textured finishes.
Beyond the Basics: Experimentation and Regional Variations
The story of sewing machine foot finishes isn't solely about brass, steel, and nickel silver. Manufacturers experimented with other coatings and techniques. Some used bronzes and bronzes with protective lacquers, while others employed decorative etching or engraving. Moreover, regional variations existed. European manufacturers, for example, sometimes favored different finishes compared to their American counterparts. Researching these nuances can be an endlessly fascinating endeavor, uncovering hidden histories and appreciating the diversity within this seemingly narrow category of crafting tools.
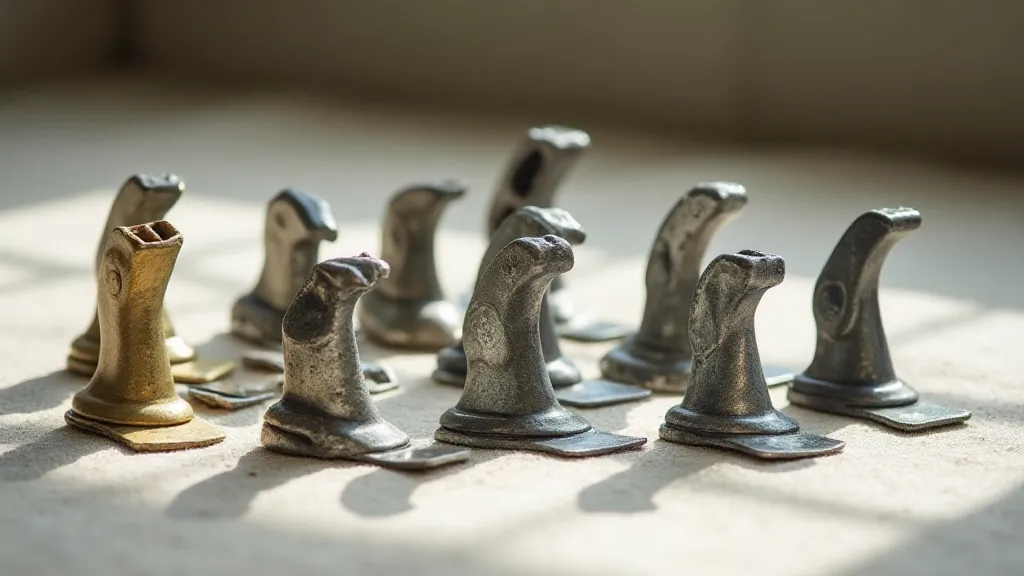
The Impact of Mass Production and the Shift in Aesthetics
The post-World War II era marked a significant turning point. The relentless push for mass production led to a simplification of finishes. Chrome plating became prevalent, offering a durable and easily applied coating. However, this often came at the expense of the handcrafted feel and the unique character that characterized earlier feet. While chrome offered a sleek, modern appearance, many purists lament the loss of the warmth and individuality that defined the pre-mass production era. The focus shifted from artistry to efficiency, and the subtle nuances in color and finish were often sacrificed in the pursuit of lower costs.
My grandfather, a tailor by trade, had a box of old sewing machine feet he kept tucked away in his workshop. He's long gone now, but I still have that box. Sometimes, when I’m feeling overwhelmed by the relentless pace of modern life, I’ll take it out and examine those tiny pieces of history. Each one reminds me of a time when things were made with care, with a respect for craftsmanship that seems almost lost in today's world.
Collecting and Restoration: Preserving a Legacy
For collectors, the variations in color and finish are key indicators of age, rarity, and manufacturer. A pristine, highly polished brass foot from the 1880s is considerably more valuable – and far more desirable – than a later, mass-produced chrome-plated foot. For those interested in restoration, understanding the original finish is crucial. Improper cleaning or refinishing can significantly devalue a foot and erase its historical significance. The goal is to preserve, not to alter, the patina and the marks of time.
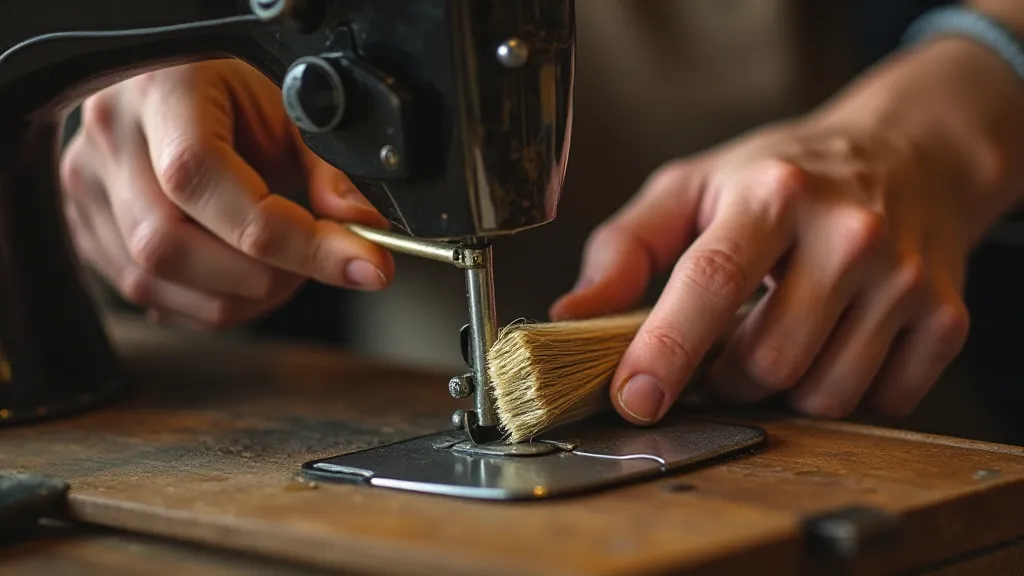
Ultimately, appreciating the evolution of color and finish on vintage sewing machine feet isn't just about the aesthetics. It’s about understanding the history of manufacturing, the changing values of society, and the enduring legacy of human ingenuity. It’s about recognizing the beauty in the small details and the stories they tell. And it's about honoring the hands – both the makers and the users – that shaped our crafting heritage.